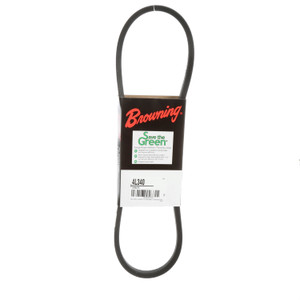
Belt Furnace: Efficient Heat Treatment Solutions for Various Industries
Heat treatment is a crucial industrial process used to enhance the properties of materials, such as metals and ceramics, by subjecting them to controlled heating and cooling cycles. Among the various equipment employed for this purpose, the belt furnace stands out as an efficient and versatile solution. In this comprehensive guide, we will explore the intricacies of belt furnaces, their applications across diverse industries, and address some frequently asked questions about this indispensable industrial equipment.
Belt furnaces are continuous heat treatment systems designed to process a wide range of materials with precision and consistency. Unlike batch furnaces, which handle materials in discrete batches, belt furnaces continuously move materials through a controlled thermal environment, making them a popular choice in various industries. These furnaces are known for their efficiency, flexibility, and cost-effectiveness, making them indispensable in many manufacturing processes.
How Belt Furnaces Work
A belt furnace consists of a conveyor belt that carries materials through a heating chamber. The key components of a typical belt furnace include:
Conveyor Belt: The heart of the furnace, it transports materials through various thermal zones.
Heating Elements: These are responsible for generating heat within the furnace. Common heating methods include electric resistance, gas, and infrared.
Control Systems: Modern belt furnaces are equipped with sophisticated control systems that regulate temperature, belt speed, and other parameters to ensure precise heat treatment.
Cooling Zone: At the end of the conveyor, a cooling zone helps rapidly reduce the temperature of processed materials.
Applications Across Industries
Electronics
In the electronics industry, belt furnaces are commonly used for solder reflow and curing of adhesives on circuit boards. They provide consistent and controlled thermal profiles, ensuring reliable solder joints and adhesive bonds.
Automotive
Automotive manufacturers utilize belt furnaces for various heat treatment processes, such as annealing, hardening, and tempering. These furnaces are essential in producing high-quality engine components and ensuring structural integrity.
Aerospace
In the aerospace sector, precision and consistency are paramount. Belt furnaces play a crucial role in heat-treating components like aircraft engine parts and turbine blades, where specific thermal profiles are critical for performance and safety.
Solar Energy
Belt furnaces are also employed in the solar energy industry to sinter photovoltaic cells, ensuring they can efficiently convert sunlight into electricity. The precise temperature control of belt furnaces contributes to the quality and efficiency of solar panels.
Advantages of Belt Furnaces
Consistency: Belt furnaces provide a uniform and controlled thermal environment, ensuring consistent results.
Efficiency: Their continuous operation minimizes downtime and increases production rates.
Cost-Effective: Compared to batch furnaces, belt furnaces are cost-effective, especially for high-volume production.
Flexibility: They can handle a wide range of materials and process variations.
Selecting the Right Belt Furnace
Choosing the right belt furnace for your application requires careful consideration of factors such as material type, size, production volume, and desired thermal profile. Consult with an experienced furnace manufacturer or supplier to ensure your specific needs are met.
Maintenance and Safety
Proper maintenance is essential to keep a belt furnace operating at peak efficiency. Regular inspections, cleaning, and calibration of control systems are crucial. Safety protocols, such as temperature monitoring and emergency shutdown procedures, should also be in place to protect personnel and equipment.
Conclusion
Belt furnaces have become indispensable in various industries, providing efficient and precise heat treatment solutions. Their ability to handle a wide range of materials and applications makes them a valuable asset for manufacturers striving to maintain quality and consistency in their processes.
FAQs
Here are some frequently asked questions about belt furnaces:
Q1: What materials can be processed in a belt furnace?
Belt furnaces can handle a wide range of materials, including metals, ceramics, and composites. The specific materials processed depend on the furnace design and application.
Q2: How do I control the temperature in a belt furnace?
Temperature in a belt furnace is controlled through the use of heating elements, sensors, and a sophisticated control system. Operators can set and monitor the desired temperature profiles.
Q3: Are belt furnaces energy-efficient?
Yes, belt furnaces are energy-efficient due to their continuous operation and precise temperature control, which minimizes energy wastage.
Q4: Can belt furnaces be customized for specific applications?
Yes, many manufacturers offer customization options to tailor a belt furnace to the unique requirements of a particular application.
Q5: Are there safety considerations when using belt furnaces?
Yes, safety protocols are essential when operating belt furnaces, including temperature monitoring, emergency shutdown procedures, and proper training for personnel.
Q6: What is the typical maintenance schedule for a belt furnace?
Maintenance schedules vary depending on usage and specific furnace models but generally include regular inspections, cleaning, and calibration.
Q7: Can belt furnaces be used for small-scale production?
Yes, belt furnaces are adaptable and can be used for both small-scale and high-volume production, making them versatile for various manufacturing needs.
Q8: How do belt furnaces compare to batch furnaces?
Compared to batch furnaces, belt furnaces offer continuous processing, higher efficiency, and lower operational costs for high-volume production.
In conclusion, belt furnaces have revolutionized heat treatment processes across multiple industries. Their versatility, efficiency, and consistent results make them a preferred choice for manufacturers aiming to achieve precise and reliable material properties. If you have any more questions or specific requirements, consult with a furnace manufacturer or supplier to find the ideal solution for your unique application.