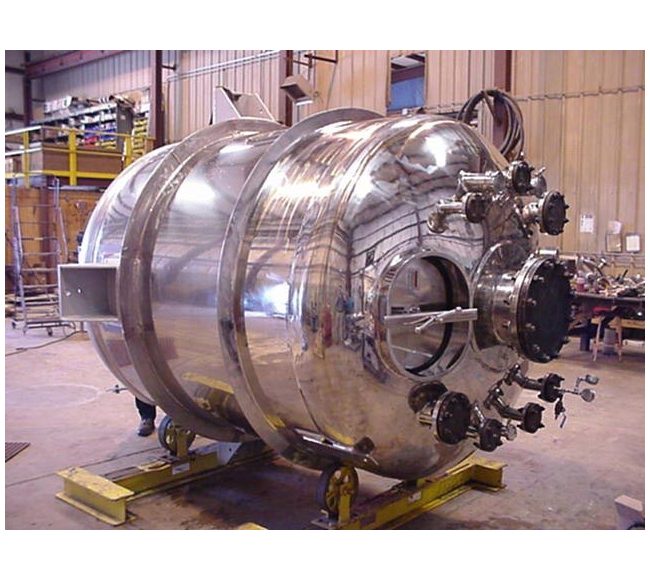
Why Coolant is Used in Chemical Reactors?
The fission reactions that generate nuclear power produce a large amount of thermal energy, which must be dissipated or the reactor could melt. Coolant circulates through the reactor core and into steam generators to remove this heat and transfer it to electricity-generating turbines.
Suitable coolants must have low neutron capture cross sections and not cause excessive corrosion of structural materials. They also must have high melting and boiling points to reduce the likelihood of a loss-of-coolant accident.
Water
Water is used for two reasons in nuclear reactors: as coolant and as neutron moderator. Nearly all commercial nuclear power plants use light-water reactors (LWRs), which use normal water as both coolant and moderator. Light-water isn’t just water you’d find in your kitchen faucet, either — it’s carefully controlled to ensure that the chemistry of the water doesn’t promote corrosion or cause a buildup of minerals in the system.
In LWRs, heated water circulated through the primary circuit picks up heat from nuclear fission, carries it to the steam generator where it is turned into high-pressure steam, and then pumps this to the turbines to generate electricity. The steam from the turbines is then returned to the reactor, turning the reactors for sale core back into hot water for more fission and more energy.
The temperature of the primary coolant is maintained by regulating valves that throttle the flow of water to and from the reactor, depending on steam demand. The boron and cadmium control rods in the reactor keep the temperature of the primary coolant from rising too quickly, reducing the power output of the nuclear fission reaction.
The main downside of using water as a coolant in a nuclear reactor is that the water must be very highly pressurized to remain liquid at such high temperatures. This requires large, heavy pipes and a high pressure reactor vessel, which increases the cost of constructing a nuclear plant. Moreover, the high pressure raises the consequences of any loss-of-coolant accident, which can damage the vessel.
Liquid Metals
Metals are earth-abundant elements with remarkable conductive and mechanical properties that find wide use in wires, thermal conductors, structural frames and pipes, coatings, catalysts and medicines. Ninety-one of the world’s eighteen metallic elements are in their liquid state at room temperature, including gallium (Ga), francium (Fr) and caesium (Cs). These fluid metals have bulk viscosities comparable to water, making them easy to manipulate into shapes that facilitate microfluidics, stretchable or injectable electronics and reconfigurable devices.
Liquid metals’ amorphous, non-crystalline atomic structure also makes them non-magnetic. The lack of grain boundaries eliminates grain-boundary corrosion — a problem that can be exacerbated in high-strength alloys produced by precipitation hardening and sensitized stainless steels. The combination of mechanical toughness, elasticity and corrosion resistance is drawing interest in the emerging field of liquid metals.
For nuclear reactors, liquid metals are attractive because they can be easily pumped through the primary circuit to cool the core and absorb neutrons that have been scattered by the fissile material in the reactor. The high scattering and low absorption cross sections of liquid metals make them more likely to be transported across the reactor walls and into the reactor vessel, where they can then be absorbed by a heavy water moderator if needed. Sodium-naK eutectic alloy is currently used as the coolant in nuclear reactors, although researchers are studying molten lead and other liquid metals as potential replacements for water.
Molten Salt
Molten salt is an interesting choice for coolant because it can withstand much higher temperatures than water. This allows it to efficiently convert heat into electricity. It also can do this without using pressurized steam, a major cost saving feature.
While the molten salt reactor concept was originally developed at Oak Ridge National Laboratory in the 1950s, it never made it into commercial power plants. Its problems could not be overcome in time to make molten salt reactors viable as power generators.
A molten salt reactor uses a mix of table salt and other chemical additives to create a working fluid that serves multiple functions: coolant, fuel, and fission product absorption. The salts used in a molten salt reactor are inexpensive, nontoxic, and easily transportable. Table salt is one of the constituents that many reactor developers are considering for their molten salt systems.
In a typical molten salt reactor design, nickel-chromium alloy fuel tubes are three-quarters filled with a molten salt mixture (60% NaCl, 40% Pu, U & lanthanide trichlorides). The salt is then grouped into assemblies and placed in a stainless steel tank called a moderator. The assembly is vented so that the fission products escape into the salt pool, where they are diluted with the molten salt. This dilution allows the molten salt to absorb stray neutrons and reduce the likelihood of nuclear fission.
Gases
The reactors in which chemicals are made in industry can vary in size from those on a desktop to the vast structures depicted in photographs of industrial plants. These can hold, at any one time, hundreds of tonnes of materials and are designed to perform particular chemical reactions. The design is determined by many factors, not least the thermodynamics and kinetics of the reactions themselves. buy reactors from surplusrecord.
There are two main types of reactor; batch and continuous. In a batch process reactants are fed into the reactor at one point, allowed to react and then withdrawn at another point. There must be an equal rate of flow in and out for the process to reach a steady state. Water softening is a simple example of this process. Hard water flows into a tube containing an ion exchange resin, the reaction takes place down the tube and soft water pours out the other end.
In a continuous process the reaction may take place in the same vessel as the storage of the products. This is the case in the steam reforming of natural gas to produce hydrogen that is used in industrial synthesis and as an energy carrier and energy storage. Currently, it is also being used to make ammonia. This is a highly exothermic reaction but it can be controlled much more readily with a closed system because the heat that would be lost by the evaporation of liquid water to the atmosphere is retained within the reaction vessel.